Formwork plywood is a crucial component in construction projects, especially in the context of concrete work. Its durability, strength, and versatility make it an essential material for creating temporary molds, or formwork, which shape and support concrete structures until they harden. However, not all formwork plywood is created equal. To ensure quality, safety, and efficiency in construction, certification and adherence to standards are of paramount importance.
Understanding Formwork Plywood
Definition and Uses of Formwork Plywood
Formwork plywood is a specialized type of F14 plywood that is designed and manufactured for the specific purpose of construction formwork. It is typically made from layers of thin wood veneers bonded together using synthetic resins. This construction-grade plywood possesses unique characteristics that make it suitable for bearing the weight and pressure exerted by wet concrete during the casting process.
Formwork plywood is extensively used in various concrete structures such as foundations, walls, columns, beams, and slabs. It provides the necessary support, shape, and containment required for pouring and molding concrete until it cures and gains sufficient strength to stand on its own. Learn more how formwork plywood contributes to sustainable building practices.
But let’s dive deeper into the world of formwork plywood and explore the different types available in the market today.
Different Types of Formwork Plywood
There are several types of formwork plywood available in the market today, each designed to meet specific construction requirements. The most common types include:
Structural Plywood
This formwork plywood is manufactured with high-grade veneers and resins to withstand heavy loads and pressure during construction. It is engineered to provide exceptional strength and stability, making it ideal for projects that require robust formwork.
Marine Plywood
Marine plywood, known for its moisture resistance, is suitable for projects with high humidity or where water contact is expected. It is constructed with waterproof adhesive and can withstand prolonged exposure to moisture without compromising its structural integrity.
Shuttering Plywood
Shuttering plywood is specifically designed for formwork projects requiring smooth concrete surfaces. It is manufactured with a smooth surface finish, minimizing the need for additional surface treatments. This type of plywood ensures a flawless concrete finish, making it popular in architectural projects.
Film-Faced Plywood
Film-faced plywood is coated with a phenolic film to enhance its durability, water resistance, and smoothness. It is commonly used in projects where high-quality finishes are desired. The film not only protects the plywood from moisture and wear but also provides a smooth surface for the concrete, resulting in a polished and visually appealing end product.
Each type of formwork plywood has its own unique properties and advantages, allowing contractors and builders to choose the most suitable option for their specific construction needs. Whether it’s the strength of structural plywood, the moisture resistance of marine plywood, the smooth finish of shuttering plywood, or the aesthetic appeal of film-faced plywood, formwork plywood offers a versatile solution for a wide range of construction projects.
By understanding the different types of formwork plywood available, construction professionals can make informed decisions and ensure the success of their projects. The right choice of formwork plywood can contribute to efficient construction processes, improved structural integrity, and exceptional concrete finishes.
The Role of Certification in Formwork Plywood
Why Certification Matters
Certification plays a crucial role in ensuring that formwork plywood meets established industry standards and regulatory requirements. This certification guarantees that the plywood has undergone rigorous testing for strength, durability, and usability. It gives construction professionals the confidence that they are working with a reliable and safe material.
Inadequate or substandard formwork plywood can result in construction delays, structural failures, and compromised safety. By using certified plywood, construction projects can avoid costly rework, repairs, and potential legal liabilities.
Moreover, certification also promotes sustainability in the construction industry. Certified formwork plywood often comes from responsibly managed forests, ensuring that the plywood is sourced ethically and does not contribute to deforestation. This eco-friendly aspect of certified plywood aligns with the growing demand for sustainable building materials in modern construction projects.
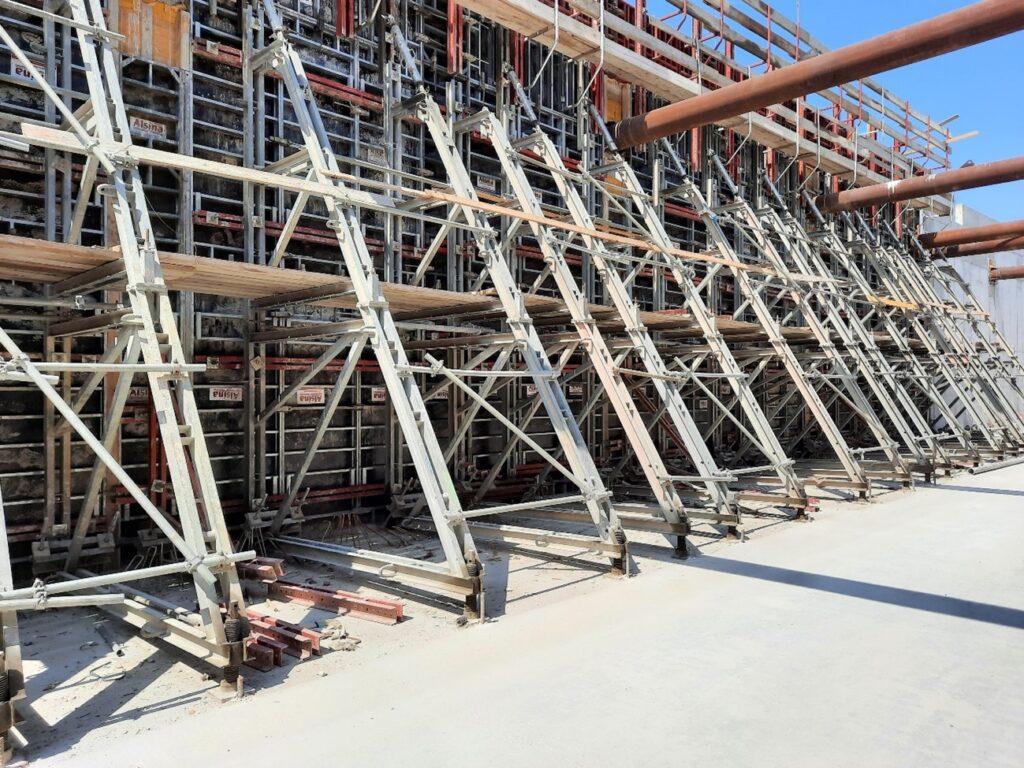
The Process of Plywood Certification
The certification process involves independent testing and evaluation of the formwork plywood by accredited certification bodies. These bodies assess the plywood against specific criteria, including dimensional tolerances, bonding strength, moisture resistance, and load-bearing capacity.
Furthermore, the certification process may also include on-site inspections of plywood manufacturing facilities to ensure compliance with quality control measures and production standards. This comprehensive evaluation process helps maintain the integrity of the certification system and provides an extra layer of assurance to construction professionals and project stakeholders.
Once a plywood product successfully passes all the required tests, it is granted a certification mark or label. This mark serves as a visual assurance of the plywood’s compliance with quality standards and its suitability for formwork applications.
Standards in Formwork Plywood
International and National Standards
Formwork plywood is subject to various international and national standards that define its quality requirements. These standards ensure consistency, reliability, and safety in construction practices across different geographical regions.
International standards, such as those established by the International Organization for Standardization (ISO), provide a framework for evaluating the performance characteristics of formwork plywood on a global scale.
National standards, such as those developed by the American National Standards Institute (ANSI) in the United States or the British Standards Institution (BSI) in the United Kingdom, establish country-specific requirements and guidelines for formwork plywood.
Formwork plywood standards are not only limited to ISO, ANSI, and BSI but also encompass regional standards set by organizations like the European Committee for Standardization (CEN) and the Standards Australia. These regional standards further refine the specifications for formwork plywood based on local construction practices, environmental conditions, and regulatory requirements.
Compliance with international and national standards is essential for ensuring the quality, safety, and performance of formwork plywood in construction projects worldwide. These standards serve as a benchmark for manufacturers to produce plywood that meets the stringent criteria set forth by regulatory bodies and industry experts.
How Standards Impact Quality and Safety
Adherence to standards ensures that formwork plywood meets specified quality benchmarks. These standards address crucial aspects such as material composition, dimensions, strength, moisture resistance, and tolerance limits.
By conforming to these standards, manufacturers, suppliers, and construction professionals can ensure the structural integrity and durability of formwork plywood. Standards also promote consistency, compatibility, and interoperability among different plywood products, allowing for seamless integration on construction sites.
Moreover, adherence to standards not only enhances the quality of formwork plywood but also contributes to improved safety on construction sites. Plywood that meets established standards is less likely to fail under load, reducing the risk of accidents and injuries during the construction process. Standard-compliant plywood also ensures that structures are built to withstand environmental factors, ensuring long-term stability and safety for occupants.
The Relationship Between Certification and Standards
How Certification Upholds Standards
Certification acts as a tangible verification that the formwork plywood meets the requirements set forth by industry standards. It provides an independent and unbiased evaluation of the plywood’s compliance and performance capabilities, giving construction professionals the peace of mind that they are working with a reliable product.
Certification enhances accountability in the supply chain as it requires manufacturers to consistently produce plywood that meets the established standards. It fosters a culture of quality and adherence to best practices throughout the plywood production process, from sourcing raw materials to the final product delivery.
Furthermore, certification plays a crucial role in promoting sustainability within the construction industry. By ensuring that formwork plywood meets specific environmental standards, certification encourages the use of responsibly sourced materials and eco-friendly production processes. This not only benefits the environment but also aligns with the increasing demand for sustainable building practices.
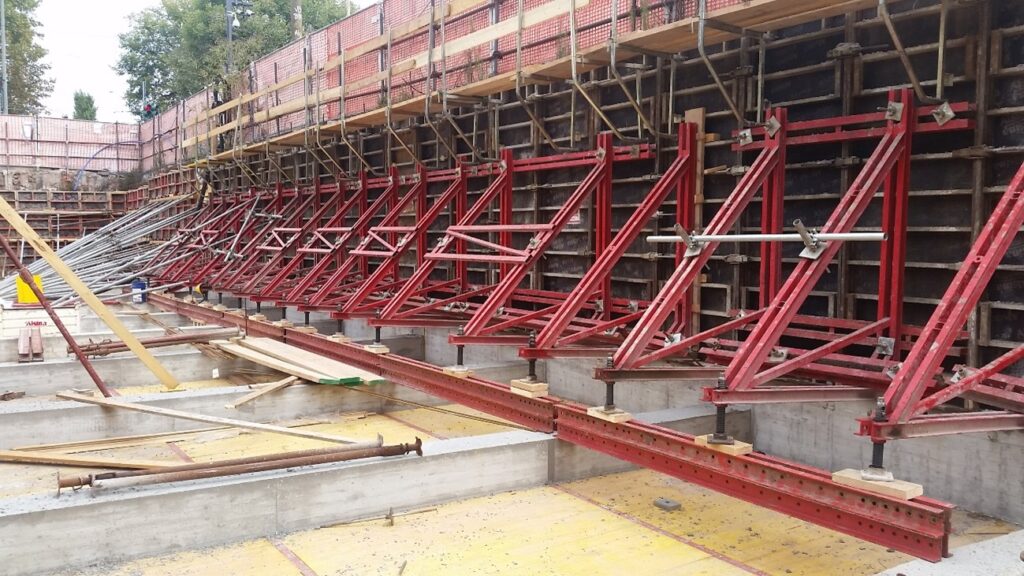
The Consequences of Non-Compliance
Non-compliance with certification and standards can have severe consequences in the construction industry. Plywood that does not meet the required quality benchmarks may compromise the structural stability and safety of concrete structures, posing risks to workers and the public.
Construction projects using non-compliant plywood may face delays, costly rework, and potential legal liabilities. Moreover, the credibility and reputation of the organizations involved can suffer significant damage.
It is essential for all stakeholders in the construction industry to prioritize compliance with certification and standards to ensure the safety, quality, and sustainability of their projects. By upholding these benchmarks, construction professionals can build with confidence, knowing that they are contributing to a safer and more reliable built environment for all.
Future Trends in Formwork Plywood Certification and Standards
Technological Advancements and Their Impact
Advancements in technology are revolutionizing formwork plywood certification and standards. With the advent of automated testing equipment and artificial intelligence, testing and evaluation processes are becoming more efficient, accurate, and reliable.
These technological advancements enable quicker and more comprehensive assessment of formwork plywood, ensuring that it meets the evolving quality demands of the construction industry.
Moreover, the integration of Internet of Things (IoT) devices in formwork plywood manufacturing is enhancing real-time monitoring and quality control. IoT sensors embedded in plywood panels can provide data on factors like moisture content, temperature, and structural integrity, allowing for proactive maintenance and quality assurance.
As the industry embraces Industry 4.0 principles, formwork plywood manufacturers are exploring the use of blockchain technology to create transparent and immutable certification records. Blockchain ensures the traceability of plywood products throughout the supply chain, enhancing accountability and trust among stakeholders.
Changes in Regulatory Landscape
The regulatory landscape governing formwork plywood certification and standards is continually evolving to address emerging challenges and industry advancements. Regulations are adapting to ensure that formwork plywood remains safe, sustainable, and environmentally friendly.
Efforts are also being made to harmonize international standards and certification processes. This harmonization promotes collaboration and fosters a global culture of quality and safety in the construction sector.
Furthermore, the shift towards sustainable practices is influencing certification criteria, with a growing emphasis on the use of eco-friendly materials and production methods. Certifying bodies are increasingly considering the environmental impact of formwork plywood, encouraging manufacturers to adopt greener alternatives and reduce carbon footprint.
In this dynamic regulatory environment, industry stakeholders are encouraged to stay informed about the latest updates and requirements to ensure compliance and uphold the integrity of formwork plywood products.
In conclusion, certification and adherence to standards are indispensable for ensuring the quality, safety, and efficiency of formwork plywood in construction projects. By using certified plywood and complying with established standards, construction professionals can confidently build robust and reliable concrete structures that withstand the test of time.